Fanali saldati a ultrasuoni degni di KITT (e David Hasselhoff)
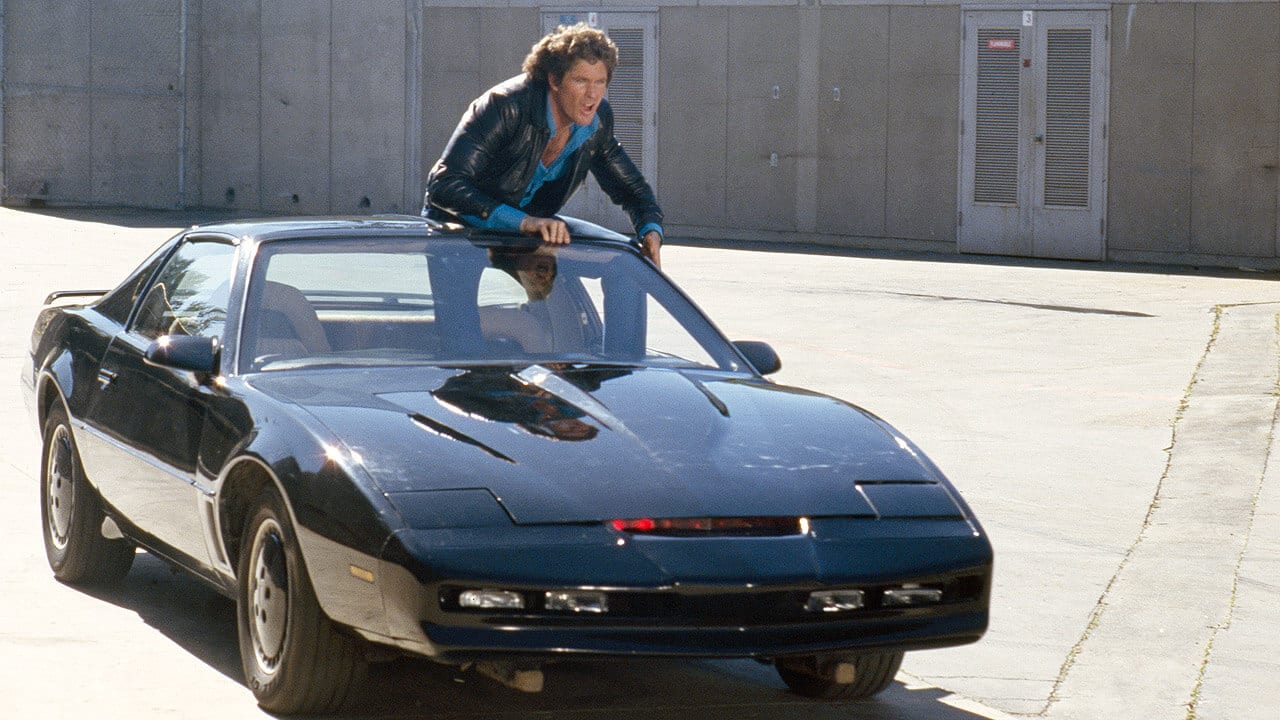
Ti è mai capitato di aver preparato tutto nel migliore dei modi, i pezzi, il sonotrodo, il posaggio e tutto il setup della saldatrice e nel preciso momento in cui fai la prima saldatura ti accorgi che niente è come l’avevi previsto?
Provi, riprovi e continui senza arrivare al risultato che ti aspettavi?
Il mio amico Victor ripete spesso le parole del suo mentore, che oltre 30 anni fa nella sua piccola officina diceva sempre: “Negli ultrasuoni l’unica certezza è che non ci sono certezze!”.
Sarà proprio così vero anche nel 2020 in cui la tecnologia ha fatto passi da gigante specialmente nell’elettronica e nel software?
Conosco Victor da 10 anni ed esattamente dal 2011. Victor (chiamato scherzosamente dai colleghi Don Victor Saldatore per la grande sicurezza e conoscenza della saldatura a ultrasuoni e a vibrazione) come molti brillanti tecnici italiani è in realtà un persona con un carattere estremamente riservato e modesto. Probabilmente è uno degli ultimi “tecnici globali” dell’Automotive in Italia. Non tanto per la sua vasta conoscenza degli ultrasuoni sia a livello teorico che pratico perché è uno dei pochissimi tecnici rimasti che è perfettamente in grado di progettare, produrre (manualmente con qualsiasi macchina utensile) e testare i sonotrodi.
La sua esperienza è iniziata circa 40 anni fa proprio in un’azienda che produceva conto terzista sonotrodi e altri utensili per le saldature plastiche nel campo automotive. Ha continuato poi ad occuparsi di saldatura estendendo le sue conoscenze ed esperienze alla vibrazione di cui è tuttora uno dei più grandi esperti a livello nazionale.
Victor è un esperto di saldatura a ultrasuoni specialmente nel settore del lighting automotive, settore di cui è occupato per buona parte della sua carriera lavorativa.
Erano già parecchi mesi che l’avevo invitato a venirmi a trovare in laboratorio per testare qualche bella saldatura complessa e critica con le nuove saldatrici servo di cui disponevo.
Negli ultimi anni si è parlato molto di come i servo motori stanno soppiantando gradualmente le classiche tecnologie della pneumatica e dell’idraulica perché offrono vantaggi incontestabili come la precisione millesimale e la possibilità di un controllo programmabile, istante per istante, secondo le proprie necessità. Le chiavi del successo di questa tecnologia elettrica sono fondamentalmente 2:
- Semplicità: il motore elettrico è formato da un rotore interno che gira sotto l’azione di un campo elettrico che ruota. L’usura è minima perché le parti in contatto sono limitate. Basta pensare ai motori dei treni che possono viaggiare per milioni di chilometri con velocità di punta superiori a 400 Km/ora
- Flessibilità: grazie ai moderni microprocessori multi-core il software di controllo dei servo motori può essere creato a piacimento e il tutto viene eseguito in frazioni di secondo.
Negli ultrasuoni, in cui i cilindri pneumatici l’hanno sempre fatta da padroni, l’avvento dei servo motori permette di controllare il processo in modo attivo perché il particolare viene guidato con una o più velocità di fusione specifiche permettendo una più precisa ricombinazione molecolare dei polimeri.
I vantaggi sono fondamentalmente 3:
- La variazioni dovute alle diverse condizioni di stampaggio vengono ridotte fino al 86% così il processo è nettamente più stabile e controllato
- La quota è controllata in modo diretto con precisione millesimale (cosa non ottenibile con la normale pneumatica); basti pensare all’estrema precisione delle macchine utensili che lavorano con 5 o 6 assi con la precisione nell’ordine dei micron
- La forza è anch’essa controllata in modo diretto tramite una cella di carico con in parallelo un controllo dell’assorbimento di corrente (controllo di coppia); in questo modo si garantisce il totale controllo sulla massima forza che può essere applicata durante la fase di saldatura
Da questa base è nato il sistema Active Melting Drive che guida in modo attivo la fusione dei due elementi e riconosce istantaneamente le criticità di ogni singolo processo.
Finalmente si è presentata l’occasione di testare il nuovo sistema con le luci targa di una SUPERCAR che devono resistere alle possenti accelerazioni e sollecitazioni di un motore 12 cilindri da 800 cavalli.
Criticità principale era la combinazione di materiali particolarmente ostici da saldare a ultrasuoni come PC+ASA con PMMA.
Il motivo principale per cui è stato scelto questo particolare di polimero è la necessità di avere un materiale molto resistente nel tempo, coriaceo contro le intemperie. Non doveva risentire dei raggi UV e doveva resistere soprattutto alle alte temperature (tipiche degli scarichi importanti delle SUPERCAR) e a forti accelerazioni e decelerazioni.
Naturalmente la saldatura doveva essere di un’estetica estrema senza bave, imperfezioni o difetti di planarità.
Queste luci targa sarebbero state accuratamente messe sotto la lente di ingrandimento della qualità Ferrari che ne avrebbe verificato la tenuta ermetica e la simmetrica proiezione della luce. I test climatici finali avrebbero testato in modo definitivo la solidità del legame molecolare PC+ASA con PMMA.
Il pezzi sono piccoli…estremamente piccoli…e chiedono solo il massimo dei requisiti tecnici in fatto di estetica e funzionalità.
I catadiottri vengono saldati in 2 processi distinti:
-
Saldatura del corpo con la lente
-
Saldatura del corpo (lente incorporata) col coperchio posteriore
-
Saldatura corpo (ASA+PC) con lente (PMMA)
Sicuramente il processo più critico della giornata.
Non solo perché ogni minima imperfezione si nota ad anni luce di distanza ma anche perché l’allineamento così come la tenuta ermetica sono strettamente richiesti.
Gli utensili sono composti da un sonotrodo in alluminio (??!) e un posaggio con una piccola leva per essere sicuri del corretto posizionamento.
Le prime prove col booster da 1:1,5 non sono incoraggianti.
La fusione non è costante, le bave la fanno da padrone e l’aspetto estetico è più da Panda che da Ferrari.
C’era bisogno di ridurre il tempo di saldatura e aumentare l’ampiezza in modo da avere un inizio di fusione dopo pochi millisecondi dall’inizio della vibrazione ultrasonica in modo da evitare che si generasse troppo materiale fuso.
La perfetta fusione doveva avere l’aspetto di un unico profilo nero/grigio in cui i 3 materiali fosse fusi ma non sovra-saldati.
Il sonotrodo ha subito mostrato qualche lacuna. Con il booster da 1:2 non vibrava. Infatti la casa costruttrice (B.) dichiarava un booster massimo di 1:1,5.
Quando ti consiglio sempre di lavorare con sonotrodi in titanio un motivo c’è. Per i sonotrodi fatti in Italia già è difficile sapere in modo preciso l’amplificazione, figurati che dicono anche qual è la massima ampiezza di lavoro possibile. E se per qualche ragione ti dovesse servire più ampiezza?
Ogni tanto mi chiedo perché tutte queste aziende di ultrasuoni spingano i clienti a comprare sonotrodi in alluminio. Quanti ricambi hai dovuto comprare negli ultimi anni?
“u capisc a me…ahi ahi ahi ahi!”
Hai capito! Soprattutto per i sonotrodi con dimensioni ridotte chiedine sempre uno in titanio, durerà di più
Cosa fare allora per avere più ampiezza?
Semplice, un vecchio trucco degli ultrasuonatori termine coniato da un mio cliente qualche anno fa…
Basta ridurre la forza di torsione nell’accoppiamento dello stack sonico (convertitore-booster-sonotrodo) dai classici 100 Nm a 90 Nm…e adesso magicamente il sonotrodo funziona anche se meglio non abusarne troppo.
In più, il setup speciale della rampa di ampiezza del sonotrodo ci ha fornito già 22 micron dopo soli 39 millisecondi, insomma una fucilata a ultrasuoni!
Un altro aspetto da migliorare è il così detto fitting: ovvero il posaggio non assicurava un contenimento corretto, il pezzo era un po’ lasco. Alcuni spessori da 0,05 mm e da 0,1 mm hanno risolto temporaneamente la situazione.
Prima di lasciarti al report parametrico che trovi qui sotto, eccoti alcuni sorprendenti dati del setup.
Il risultato finale è stato perfetto ma mi ha personalmente riservato alcune sorprese.
- Forza di trigger 190 N, circa il 300% rispetto al teorico
- Ampiezza 36 micron (valore di picco), il 70% in più del teorico
- Massima forza e reattività del motore a 3.000 N
- Velocità di fusione 3,4 mm/s, il 150% del teorico (più veloci anche dei semicristallini!)
- Profondità relativa di fusione 0,25 mm più 0,10 mm in fase di mantenimento
- Raffreddamento con forza di 250 N per 0,8 secondi
Il tutto con un tempo di saldatura compreso tra 58 e 63 millisecondi (!!!) anche più veloce di una Ferrari…
- Saldatura corpo (lente incorporata) con coperchio posteriore
In questo caso il lavoro è stato più semplice.
Grazie all’esperienza dei test precedenti sono riuscito a trovare il setup corretto in meno di un’ora.
Il questo caso il posaggio era stato realizzato con tolleranze corrette ma, troppo bello per essere vero (!!) il sonotrodo è stato realizzato con uno dei più tipici errori progettuali.
Facciamo un piccolo gioco. Trova l’errore!
Con un design piano, in fase di raffreddamento il sonotrodo si appoggia contro la cornice esterna e improvvisamente la tua Forza di mantenimento va a 0!
Morale della favola il materiale non viene compresso a sufficienza e la tenuta meccanica è chiaramente molto inferiore dell’attesa. In più gratis puoi ottenere delle bellissime zone di vuoto che minacciano selvaggiamente la tenuta ermetica. Tutto chiaro?
Ecco un piccolo schema che riassume la situazione.
Per compensare questo problema del sonotrodo senza dover rilavorare l’utensile abbiamo ridotto la quota di saldatura relativa, aumentato l’ampiezza e ridotto la velocità di fusione.
Il risultato è stato raggiunto con successo con qualche piccolo trucchetto parametrico ma una tirata d’orecchie a chi ha designato il sonotrodo la diamo comunque!
Ecco un piccolo report parametrico con i consigli su come dovrai fare tu.
- Forza di trigger 260 N, il 40% in più del teorico
- Ampiezza 38 micron (valore di picco), 80% in più del teorico (!!!)
- Massima forza e reattività del motore a 3.000 N
- Velocità di fusione 1,2 mm/s, in linea con le attese
- Profondità relativa di fusione 0,41 mm più 0,12 mm in mantenimento (situazione di blocco)
- Raffreddamento con forza di 650 N per 0,8 secondi
Come avrai potuto notare, per poter fondere abbastanza materiale per ottenere una tenuta meccanica adeguata anche in presenza di un design non corretto del sonotrodo, ho dovuto ridurre la velocità di fusione fino a 1,2 mm/s e quindi anche l’effetto del “drop in force” è più evidente.
Approfondirò il fenomeno del “drop in force” in un altro articolo. Per il momento sappi che è l’effetto provocato dalla vibrazione ultrasonica a un elemento soggetto a una forza di compressione.
Semplicemente la parte tende a collassare su se stessa per effetto dell’inizio della fusione.
La criticità in questo è che il sonotrodo tende a perdere contatto col particolare se non hai un sistema specifico che si adatti in tempo reale alla velocità con cui l’elemento superiore fonde e compenetra la parte inferiore.
Se continui ad avere problemi, puoi sempre chiamare.
In bocca al lupo e buone saldature!
Francesco
Lascia un commento