Introduzione alla saldatura a ultrasuoni: i 3 driver fondamentali
Esistono differenti tecniche di saldare o tagliare particolari plastici.
Si possono utilizzare ad esempio: la vibrazione lineare, il laser, la lama calda, l’alta frequenza, l’induzione e così via.
In questo blog si parla solo degli ultrasuoni utilizzati nel mondo plastico: saldatura, taglio, sigillatura, punzonatura, taglio&saldatura. Dalle classiche saldature di due elementi termoplastici, al taglio alimentare, alla saldatura delle membrane fino a soluzioni di sigillatura.
Una specializzazione che al suo interno richiede un numero così elevato di concetti, applicazioni e metodologie che il giorno in cui si finirà di imparare sicuramente è ancora molto lontano.
Solo alcuni anni fa certe applicazioni erano impensabili utilizzando gli ultrasuoni.
Coi moderni sviluppi si posso avere generatori standard oltre i 6 kW, che controllano e retro-azionano il processo fino a 20.000 volte ogni secondo, convertitori che lavorano ininterrottamente 24 ore al giorno per 7-8 anni senza danneggiarsi o sonotrodi in acciaio temprato che pesano più di 30 kg e sono grandi come una scatola da scarpe.
Ma andiamo per ordine e cominciamo a vedere come vengono generati gli ultrasuoni e come agiscono sui particolari termoplastici.
La saldatura a ultrasuoni sfrutta il principio fisico della piezoelettricità.
Te la spiego velocemente solo per farti capire la legge naturale che sta alla base della nostra saldatura.
In natura alcuni materiali (cristalli in questo caso) hanno la caratteristica di generare un differenza di potenziale quando sono soggetti a una sollecitazione meccanica che li deforma. In questa situazione questi cristalli si comportano come un condensatore e generano una corrente.
Hai presente il vecchio accendigas che dovevi premere per accendere la fiamma con quella piccola scarica? Esatto, proprio quello.
Nella saldatura a ultrasuoni si utilizza questo principio in modo duale, cioè reversibile; semplicemente si genera una corrente ad alta frequenza che causerà nei nostri cristalli piezoceramici una deformazione dell’ordine dei micrometri (µm), ripetuta per migliaia di volte al secondo, in modo da sollecitare e portare in fusione il nostro particolare.
A livello fisico, il suono è un’onda di pressione che si trasmette nei mezzi elastici (gas, fluidi, corpi rigidi) e a seconda della frequenza questi suoni vengono classificati in infrasuoni (fino a 16 Hz), suoni udibili (fino a 16 kHz), ultrasuoni (fino a 1 GHz) e ipersuoni (maggiori di 500 MHz).
D’ora in avanti faremo sempre riferimento agli ultrasuoni e specialmente a 4 frequenze di lavoro caratteristiche, nell’ordine 20kHz, 30kHz, 35 kHz e 40 kHz.
Ora che abbiamo identificato il nostro punto di lavoro, possiamo passare a parlare degli elementi coinvolti, gli attori veri e propri della saldatura a ultrasuoni.
Possiamo considerare il processo di saldatura definito in 10 distinte fasi:
- Il generatore (a sinistra) trasforma la tensione di rete in bassa frequenza (50 Hz) innalzandola a frequenza superiore (da 20 kHz in su) con una tensione e una corrente proporzionale.
- Questa potenza elettrica a alta frequenza viene trasferita tramite un cavo coassiale apposito ad alta frequenza (al centro) al convertitore.
- Il convertitore (a destra in alto) è fatto da una parte interna di titanio, un involucro esterno in acciaio inox e all’interno ha 4 o 6 dischi di materiale piezoceramico montati in modo coassiale. Quando questi dischi (fisicamente composti di piombo-zirconio-titanio) vengono sottoposti a una determinata tensione, si dilatano e comprimono con la stessa frequenza di questa potenza elettrica. Questo avviene in modo impercettibile ad occhio umano perché le contrazioni/espansioni sono dell’ordine dei micrometri (ovvero millesimi di millimetri).
- Il convertitore trasmette le vibrazioni ad un altro elemento di amplificazione meccanica: il booster (o amplificatore).
- L’amplificatore trasferisce a sua volta le vibrazioni all’elemento di contatto coi nostri particolari: il sonotrodo
- Il sonotrodo vibrando (similmente a una molla) dal basso verso l’alto (ovvero in senso normale), trasferisce questa onda stazionaria al pezzo sottostante.
- Quest’ultimo (composto da un qualsiasi termoplastico) inizia a scaldarsi rapidamente e, nelle zone desiderate, arriva al punto di fusione.
- Il calore viene trasferito dall’interno verso l’esterno in tutta l’area di contatto (chiamata regione di giunzione) tra i due particolari: inizia una compenetrazione in cui i due materiali si fondono insieme.
- Sotto l’azione di una specifica velocità di fusione (o di una o più forze per le classiche saldatrici pneumatiche) i due particolari di uniscono.
- La vibrazione ultrasonica viene interrotta e nella fase di mantenimento i due particolari si uniscono; la giunzione si raffredda velocemente rendendo le due parti separate, un unico elemento.
Posso chiarire meglio questo concetto grazie all’analogia col funzionamento delle automobili.
Il generatore è il motore, il booster (o amplificatore) la trasmissione e le ruote il sonotrodo.
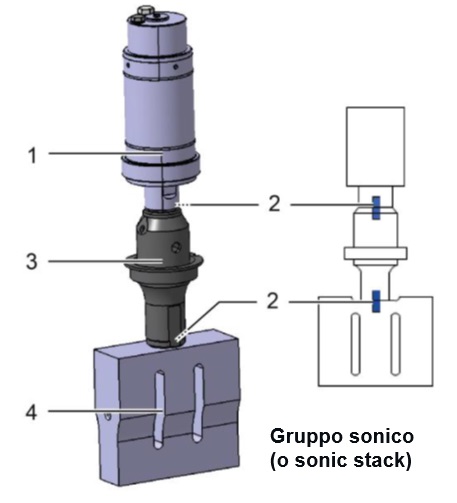
A questo punto posso immaginare che tra le tante domande che mi vorresti fare ce ne sia una del tipo:
“Ok, questo è chiaro, ma come faccio a controllare il processo di saldatura a ultrasuoni e come utilizzo gli strumenti a mia disposizione unire fisicamente i particolari?”
La risposta a questa domanda è semplice.
La sua applicazione invece è più complessa e necessita di una spiegazione approfondita che troverai qui sotto.
Per controllare il tuo processo devi utilizzare 3 elementi che in questo blog saranno chiamati driver fondamentali del processo di saldatura.
• FREQUENZA (la cui unità di misura è L’Hertz [Hz])
• AMPIEZZA (la cui unità di misura è il micron [µ])
• VELOCITÀ o Forza (la cui unità di misura è il mm/secondo o il Newton [N])
Devi saper che tutti (e voglio dire proprio tutti!) i processi di saldatura sono guidati dalla gestione e dalle modifiche dei tre driver fondamentali: frequenza, ampiezza e forza.
Probabilmente sarai sorpreso dalla mia frase precedente perché ti saresti aspettato che citassi anche il tempo o l’energia. In realtà queste grandezze e parametri di controllo vengo sempre utilizzati ma solo per gestire in modo diretto o indiretti i tre driver fondamentali.
Prima di andare avanti ti devo avvisare.
La maggior parte dei tecnici che si occupano di saldatura a ultrasuoni ha sicuramente sentito nominare queste grandezze ma, nella quasi totalità dei casi, non ha mai compreso tutte le implicazioni tecniche e applicative che queste comportano.
Per rendere il concetto più semplice pensa in questo modo:
• Frequenza = quanto spesso viene applicata la sollecitazione
• Ampiezza = quanta intensità usi (istante per istante)
• Velocità = come gestisci l’accoppiamento (saldatura) o la separazione (taglio)
Tutti gli altri parametri servono solo a gestire in modo più o meno diretto questi tre fondamentali driver.
Non voglio appesantire questo post con troppi concetti tecnici, tuttavia la comprensione di queste basi ti darà importanti informazioni che ti aiuteranno a gestire al meglio i vantaggi e, naturalmente anche i limiti di questa tecnologia.
La frequenza si differenzia dalle altre due grandezze perché essa è fissa.
Viene definita all’inizio e non può più essere modificata se non cambiando il generatore.
Come accennavo in uno dei primo post, la frequenza nella saldatura a ultrasuoni va da 15kHz a 70kHz con le dimensioni degli utensili che sono tanto più piccoli quanto più si alza la frequenza.
In Europa tipicamente si usano le frequenze di 20, 30, 35, 40 e 70 kHz.
La 15kHz è più tipica dei paesi anglosassoni e, anche se permette utensili (sonotrodi) più grandi, la bassa ripetibilità nelle applicazioni l’ha resa una risorsa marginale a cui attingere per particolari molto grandi che non richiedono precisione.
La frequenza verrà trattata in dettaglio nel post dedicato ai principi fondamentali, per ora ti posso dire che, a parità di materiale plastico, quanto più si alza la frequenza di vibrazione, tanto più diminuiscono i requisiti in termini di ampiezza per poter saldare.
Se utilizzi un PP, a 20kHz ti serviranno 38 µ, a 30kHz 32µ, a 35kHz 28µ.
Adesso andiamo ad analizzare cos’è precisamente l’ampiezza di vibrazione e quale convenzione userò d’ora in poi per definirla.
Come abbiamo visto, gli ultrasuoni nel nostro caso sono vibrazioni meccaniche che si propagano nei mezzi materiali (dal convertitore al sonotrodo) in modalità sinusoidale.
Una vera e propria onda di carattere stazionario (ovvero che oscilla attorno ad un punto fisso, aumentando e diminuendo la distanza da questo) e percorre gli elementi che compongono la struttura sonica (o sonic stack) fino ad arrivare sulla superficie del sonotrodo a contatto col pezzo.
Definiamo adesso l’ampiezza come differenza tra la massima espansione e la massima contrazione all’altezza del nostro convertitore.
Come puoi vedere dall’immagine qui sottostante, l’onda si propaga nel nostro sonic stack
dal convertitore fino alla superficie del sonotrodo a contatto col pezzo.
Adesso seguimi nel ragionamento perché questo è uno dei punti fondamentali per capire a pieno il processo di saldatura.
L’ampiezza non è altro che la grandezza con cui definiamo in termini parametrici l’ intensità della sollecitazione che stiamo imprimendo al nostro particolare. Più la sollecitazione è forte, prima lo porteremo al suo caratteristico punto di fusione (o melting point).
L’ampiezza, di conseguenza, regola anche la velocità di fusione del materiale.
Un’altra conseguenza è che per certi materiali con punto di fusione più elevato (PEEK o PA 6.6) se non arriviamo all’ampiezza necessaria, il nostro particolare si scalderà solamente senza però fondere.
Se hai capito questo allora per te sarà facile capire perché molti fornitori o produttori di saldatrici ti dicono che alcuni materiali non si possono saldare.
La risposta è che non possiedono una tecnologia sufficiente per produrre un’ampiezza adeguata oppure per garantire una potenza sufficienza a portare alla fusione completa materiali con melting point elevati.
Il limite in realtà non è la tecnologia di per se, ma il fatto che, come molte piccole aziende di provincia con pochi dipendenti e poche risorse, la maggior parte dei fabbricanti di ultrasuoni non si può permettere di sviluppare generatori più potenti e performanti per applicazioni complesse e avanzate che richiedono maggiore potenza e ampiezza.
Ora io non sto certo criticando questo tipo di attività, che sono il cuore pulsante della nostra economia, ti sto solo mettendo in guardia da quello che ti possono raccontare certi venditori e certe piccole società che, per nascondere la limitatezza dei propri mezzi o lo scarso know-how tecnico nello sviluppo delle soluzione di saldatura a ultrasuoni, scaricano il problema sulla tecnologia senza offrire una risposta professionale in termini di fattibilità.
Ultimamente anche società quotate, multinazionali del settore della saldatura plastica, sembrano meno interessate ad offrire un servizio completo e adeguato anche per soluzioni di carattere più complesso o “sperimentale”.
Insomma se vuoi comprare una saldatrice va bene, ma se chiedi un supporto più completo non sono disposti a darti il giusto supporto.
Certamente chi offre più soluzioni di saldatura (vibrazione, laser o infrarosso) ha un focus meno orientato e diretto alla saldatura a ultrasuoni rispetto a chi si è specializzato solo in quest’ambito.
Le conseguenze, come ben sai, sono spiacevoli per te che cerchi, oltre agli strumenti fisici anche il supporto tecnico completo e costante per sviluppare in modo efficiente e sicuro il tuo progetto e il tuo lavoro.
Anche per questo ho creato questo blog.
Uno spazio dedicato interamente alla saldatura a ultrasuoni professionale intesa come unica specializzazione.
Se anche tu la pensi così, questo è posto giusto in cui avere le informazioni corrette che ti consentano di sviluppare il tuo progetto in modo professionale.
Se non la pensi così, allora prova a pensare a quanti scarti hai prodotto finora, a quanti progetti hai tirato avanti mesi e mesi in attesa di una soluzione, a quante telefonate hai ricevuto dai tuoi clienti perché eri in ritardo oppure perché per colpa di alcune saldature mal eseguite lui ci ha rimesso tempo e soldi e adesso si vuole rifare su di te.
Prova a pensare a quante ore hai impieghi in logoranti cambi setup che non portavano ad avere quello che volevi, o alla commessa che hai perso perché il cliente non ha avuto da te la certezza che voleva e ha scelto un fornitore più economico.
“Se i miei fornitori sono tutti uguali, allora prendo quello che costa meno”
Questo pensa il tuo cliente quando sceglie un altro. Certo non è piacevole ma è la pura verità e se sei veramente onesto sai che anche tu fai lo stesso.
Quante volte ti sei informato o hai chiesto informazioni a varie società/persone per poi scegliere la soluzione più economica una volta che avevi le idee sufficiente chiare.
Scusa se ho divagato troppo, ma mi è sembrato doveroso chiarire questi punti per dedicare queste informazioni solo a chi è veramente interessato.
Adesso ritorniamo alla nostra tecnica e al terzo fondamentale driver, la velocità (o forza).
Fino a 4-5 anni fa le aziende disponevano solo di saldatrici pneumatiche e quindi la forza era l’unico parametro controllabile. Il processo di saldatura veniva gestito in modo passivo applicando una (o più) forza e ignorando quale fosse l’andamento reale del processo di fusione (Passive Force Profile).
Adesso coi moderni servo motori puoi decidere tu, in modo semplice, quale deve essere la velocità di fusione migliore per la specifica applicazione. Il servo motore e la cella di carico del sistema, regoleranno il processo di fusione in modo da auto-adattarsi alle condizioni di ogni singola saldatura per mantenere la velocità di fusione ideale (Active Melting Drive).
Perché è un fondamentale driver della saldatura a ultrasuoni?
La motivazione è che la velocità fa in modo di tenere insieme i due particolari prima che siano saldati finché il processo non ne decreti la totale unione. Una forza di triger li fa accoppiare e permette che la successiva velocità di fusione ottimizzi la trasmissione del calore della vibrazione ultrasonica in tutta l’area interessata.
Per rendere questo concetto più facile, prova a pensare a due pezzo in fase di saldatura come due fiumi adiacenti. Entrambi continueranno a scorrere per proprio conto finché non agirò, forzandoli con una spinta decisa e continua, a unirsi e creare un unico corso d’acqua.
Fintanto che non avrò raggiunto nuovamente lo stato solido alla fine della saldatura, la forza è il driver necessario che compatta la regione di giunzione, tiene nella posizione corretta le due parti ed evita che si creino delle aree di vuoto all’interno (magari causate da bolle d’aria) il che renderebbe molto più fragile la tua saldatura.
Inoltre nel caso di saldatura in tenuta ermetica, se non gestisci correttamente la velocità di accoppiamento avrai come problema principale la perdita di ermeticità in alcuni punti.
Le saldatrici servo elettriche sono già presenti sul mercato da parecchi anni, ma come mai non sono mai riuscite fino ad ora a soppiantare le classiche pneumatiche?
Il motivo è molto semplice.
Dovendo processare materiali termoplastici quali ABS, PC, PA o PPS la principale difficoltà è la gestione della fusione nelle regioni di comportamento non lineare.
Il servo motore gestisce il processo di saldatura in modo estremamente preciso (0,001 mm). L’aspetto correlato con la massima precisione è però la rigidità del sistema. Durante la fusione, specialmente per i materiali semicristallini, si attraversano zone di comportamento non-lineare e il processo richiede quindi un sistema che lo assecondi in tempo reale. Se il servo motore non riesce ad adattare la velocità di discesa in istantaneo ci si scontra con 2 principali problemi.
1. Il sonotrodo perde contatto con la parte e crea evidenti segni estetici sulla superficie di appoggio
2. Il materiale fuso viene espulso dalla regione di giunzione provocando bave e perdite
Per questo motivo è stata creata la struttura tenso-flettente ParalliCer®: un telaio flessibile vincolato calcolato FEM, chiamato C-frame, si comporta in modo simile a molla (“spring-load effect”). Quando il servo motore applica una determinata forza all’unità vibrante (controllata dalla cella di carico posta in posizione normale) il sistema paralliCer® si flette.
La flessione assicura che il sonotrodo sia sempre e costantemente in contatto con la parte in ogni istante, anche nelle regioni di comportamento non lineare del polimero.
Il sistema si autoregola così in tempo reale agendo sulla flessione o sulla deflessione del C-frame.
ParalliCer® permette l’utilizzo di intervalli di forze finora impensabili, da 5 N fino a 3.000 N oppure da 100 N fino a 9.000 N per la Genesis NEWTON.
Con la tradizionale pneumatica si sarebbero dovuti utilizzare almeno 4 diverse taglie di cilindri per coprire tale intervallo e nessuno di questi avrebbe potuto garantire la massima precisione su tutta la scala di valori.
In più l’assenza dell’aria compressa assicura un risparmio sia in termini energetici (specialmente per le camere bianche) che in semplicità e affidabilità delle calibrazioni.
Il più grande vantaggio delle nuove saldatrici MS SoniTOP è la combinazione tra precisione del servo motore e flessibilità dinamica del ParalliCer®.
Variazione dell’umidità, modifiche dimensionali e incompletezze dei direttori di energia vengono così facilmente identificati e compensati per la massima stabilità del processo.
Una dimostrazione pratica dell’efficienza energetica delle SoniTOP lo si può verificare in modo semplice analizzando la temperature delle parti appena saldate. L’efficiente accoppiamento sonotrodo-parte permette di mantenere il calore di fusione all’interno della regione di saldatura riducendo fino al 68% la dispersione dell’energia di plastificazione.
Le parti appena saldate sono già a temperatura ambiente e preservano in modo migliore sia le caratteristiche meccaniche che quelle dei componenti elettronici interni, dove presenti.
Uno studio effettuato presso il polo medicale di Mirandola per la saldatura di un filtro aria dimensioni 80 x 84 mm, con una membrana all’interno da comprimere per garantire la tenuta ermetica, ha fornito il seguente risultato:
• 12.124 parti saldate
• 0,12% scarti di saldatura
• 100% tenute ermetiche nei particolari testati
• Tolleranze dimensionali post saldatura: ±0.01 mm
Tutte le saldature tecniche complesse (filtri sangue, sensori, pompe centrifughe, fanali) finora analizzate nei laboratori MS di Spaichingen (GER) o di Fonte (TV) indicano chiaramente che la guida attiva del processo di fusione con la tecnologia Servo-ParalliCer® migliora l’efficienza e la stabilità dei processi se confrontata con la classica pneumatica.
Una bella differenza non credi?
Riassumendo in 3 punti chiave
- La saldatura a ultrasuoni è uno dei metodi più comunemente utilizzati per la saldatura dei termoplastici. Il principio alla base è una vibrazione normale (simile a un martellamento dall’alto verso il basso) che viene ripetuta in modo ritmico ad alte frequenze (ultrasoniche appunto, che vanno dai 15 ai 70 kHz).Questa sollecitazione, regolata per intensità (ampiezza), crea una frizione intermolecolare all’interno del materiale che a sua volta porta ad un riscaldamento localizzato.Il riscaldamento localizzato, dall’interno all’esterno, viene trasmesso successivamente alle area attigue per contatto e porta alla fusione rapida (con tempi inferiori a 0,1 s) di una definita e ben determinata area chiamata: regione di giunzione.Nella regione di giunzione, o area di contatto tra due differenti elementi o tessuti, si crea un mescolamento dei materiali (grazie a una forza di accoppiamento che spinge uno contro l’altro) che poi verranno solidificati e daranno vita all’insieme finale
- Nella saldatura a ultrasuoni ci sono due driver fondamentali, ovvero due grandezze che più di ogni altro fattore regolano il processo e i risultati: ampiezza e velocità. L’ ampiezza, primo e più importante driver, guida il processo di fusione. L’ampiezza dipende dal polimero utilizzato (a seconda se stiamo lavorando con una struttura molecolare amorfa o semicristallina) e dal melting point. Nella saldatura a ultrasuoni professionale si fissa il valore di ampiezza e lo si tiene costante; ciò che si modula è la rampa di salita e discesa al valore definito (maggiori dettagli nel post sul generatore di ultrasuoni).In questo blog si parlerà sempre di ampiezza di picco (e non picco-picco) quindi fai molta attenzione a come devi misurarla e quale riferimento userai.
- La velocità (di fusione) è il secondo driver e guida le dinamiche di accoppiamento. È responsabile della gestione, evoluzione e compressione finale del materiale fuso. Dalla sua gestione dipende l’accoppiamento tra le parti e, se mal gestita, può essere responsabile di graffi, bave, disallineamenti e anche dei difetti strutturali della regione di giunzione.
Anche in questo caso, nella saldatura a ultrasuoni professionale si parla di velocità di saldatura perché regolata in modo preciso ogni millisecondo dal nostro servo motore.
Forza e pressione sono comunque grandezze molto usate per le classiche saldatrici pneumatiche ma verranno considerate solo a scopo di confronto coi nuovi sistemi servo elettrici.
Siamo così arrivato alla fine del primo articolo sui fondamenti della saldatura a ultrasuoni.
Questo è solo l’inizio, pensa a quante altre informazioni potrai trovare nei prossimi articoli.
In bocca al lupo e buone saldature!
Francesco
salve
sto cercando in internet una saldatrice ad ultrasuoni per sigillare i tubi delle creme
non mi serve qualcosa di eccezionale ma un piccolo macchinario da laboratorio
ho visto che tu ne sai già qualcosa in materia
sapresti indicarmi qualche prodotto
ed indicarmi che costi dovrei sostenere
grazie mille
cordiali saluti
dove posso comprare l’apparecchio in fotografia ?
dovrei usarlo sfruttando le sue microvibrazioni per la pulizia ndi reti da 100 microns grazie
Abbiamo cliente interessato ad acquisto di apparecchi per la saldatura ad ultrasuoni da 15KHz 2600W,ci puo’ indicare il produttore Italiano piu’ valido?
Grazie
Ciao come faccio a sapere se l’ultrasuono funziona ovvero non salda e toccandolo mi sembra che vibri pochissimo ma esiste un sistema per provarlo???
Ciao Mauro, esistono principalmente 3 modi per verificare se la vibrazione è corretta. Il modo migliore è un laser interferometro che misura la vibrazione in vari punti con precisione di 0,01 micron. Il secondo modo è con un’analizzatore di sonotrodi e sonda di misura (questo si può fare direttamente da te in azienda) e la precisione è di 0,1 micron. L’ultimo modo è per via software. Una speciale algoritmo misura la frequenza di risonanza e la potenza assorbita a vuoto. In questo modo si vede se il consumo di potenza è anomalo oppure se ci sono frequenze di risonanza parassite che fanno vibrare in modo scorretto il sonotrodo. Specialmente i sonotrodi costruiti in modo artigianale non vengono testati con questi 3 metodi e possono facilmente vibrare in modo scorretto. Se ti serve aiuto chiamami pure allo 339-3535740. Buona giornata e in bocca al lupo per il tuo problema. Francesco